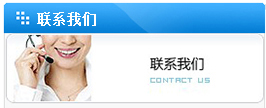 |
电 话:0533-4183588
传 真:0533-4230008
手 机:13953346669
联系人:孙要武
地 址:中国 山东淄博市博山区
邮 编:255200
|
|
当前位置:首页 - 新闻中心 - 新闻中心 - |
|
如何选择适合磨齿加工的齿轮材料硬度? |
选择适合磨齿加工的齿轮材料硬度时,需综合考虑材料的切削性能、耐磨性、热处理工艺及服役工况等因素。以下从技术原理、影响因素及实用建议三方面展开分析:
一、磨齿加工对材料硬度的基本要求
硬度与磨削性能的关系
硬度过低(<25HRC):材料塑性大,磨齿时易产生 “黏磨” 现象(磨粒被金属屑堵塞),导致砂轮寿命缩短(磨损速率可增加 30%),且齿面易出现划痕、烧伤等缺陷。
硬度过高(>60HRC):材料脆性增大,磨削时易产生微裂纹,同时砂轮磨损加剧(如磨削 62HRC 的轴承钢时,砂轮消耗速度是 45HRC 钢的 2 倍),加工效率降低。
适宜硬度区间:通常推荐 28-35HRC(调质处理) 或 58-62HRC(淬火 + 回火),兼顾切削性与耐磨性。
二、影响硬度选择的关键因素
1. 服役工况与性能需求
载荷条件:
轻载荷(如仪器仪表齿轮):可选 25-30HRC,降低加工成本(磨削效率提高 15%)。
重载荷(如工程机械齿轮):需 58-62HRC,通过高硬度提高抗接触疲劳强度(接触疲劳寿命可延长 2-3 倍)。
转速与噪音要求:
高速齿轮(>3000rpm):推荐氮化处理(60-65HRC),利用氮化层的高硬度(HV900-1200)减少摩擦发热,同时降低噪音(比调质齿轮噪音低 5-8dB)。
2. 热处理工艺可行性
淬火变形控制:
大尺寸齿轮(模数 > 5):若硬度要求过高(>60HRC),淬火时易因内外温差产生变形(变形量可达 0.1-0.3mm),需采用分级淬火或等温淬火工艺,成本增加约 20%。
表面硬化深度:
渗碳淬火齿轮:硬度需与硬化层深度匹配(如硬化层深度 0.8-1.2mm 时,表面硬度 58-62HRC),若硬化层过浅而硬度高,易发生表层剥落。
3. 加工成本与效率平衡
硬度对磨削效率的影响:
30HRC 钢的磨削比(磨除体积 / 砂轮磨损体积)约为 50,而 60HRC 钢仅为 20,即相同条件下磨削高硬度材料时,加工时间增加 1.5 倍,砂轮更换频率提高。
设备适应性:
普通磨齿机(如 Y7125):适合加工 30-45HRC 材料;
高精度数控磨齿机(如克林贝格 C65):可处理 55-65HRC 硬齿面,但设备投资成本高(约为普通设备的 3-5 倍)。
三、不同应用场景的硬度选择策略
1. 汽车工业齿轮
手动变速箱齿轮:
材料:20CrMnTi
硬度:齿面 58-62HRC,心部 30-35HRC
优势:表面高硬度抵抗换挡冲击,心部韧性防止断裂(疲劳强度≥800MPa)。
电动驱动齿轮:
材料:42CrMo
硬度:调质 28-32HRC + 感应淬火 52-55HRC
优势:降低高速运转时的磨削烧伤风险(感应淬火硬化层均匀性 ±0.05mm)。
2. 风电齿轮箱
材料:17CrNiMo6
硬度:渗碳淬火后 60-62HRC
特殊要求:需通过超声波探伤检测表层微裂纹(探伤灵敏度≥Φ0.5mm 平底孔),因高硬度下材料对缺陷更敏感。
3. 精密仪器齿轮
材料:38CrMoAl
硬度:气体氮化后 HV900-1100(约 65HRC)
优势:氮化层硬度梯度平缓(从表面到心部硬度下降≤10%),减少磨削时的应力集中,保证齿形精度(可达 ISO 4 级)。
四、硬度选择的实用建议
根据磨齿工艺类型调整:
展成磨(适合批量生产):材料硬度≤35HRC,避免砂轮快速磨损;
成形磨(适合大模数):可处理 58-62HRC,但需选用 CBN 砂轮(寿命是普通刚玉砂轮的 10 倍)。
硬度与表面粗糙度匹配:
高精度齿轮(Ra≤0.8μm):硬度控制在 58-60HRC,过高硬度易导致磨削纹路加深(Ra 可能升至 1.2μm)。
预加工工艺的影响:
滚齿后留磨量:硬度≤35HRC 时,留磨量 0.1-0.15mm;硬度 > 55HRC 时,需增至 0.2-0.25mm,补偿磨削时的砂轮损耗。
|
发布时间:2025/7/2 10:53:32 点击次数:2 |
|
|
|