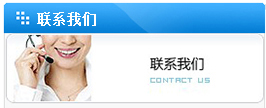 |
电 话:0533-4183588
传 真:0533-4230008
手 机:13953346669
联系人:孙要武
地 址:中国 山东淄博市博山区
邮 编:255200
|
|
当前位置:首页 - 新闻中心 - 新闻中心 - |
|
如何优化切削参数以提高齿轮加工质量? |
优化切削参数是提升齿轮加工质量的关键环节,需从切削速度、进给量、切削深度等核心参数入手,结合刀具特性、工件材料及工艺系统刚性综合调控。以下从参数影响机制、优化原则及实施策略三方面展开说明:
一、切削参数对齿轮加工质量的影响机制
1. 切削速度(v)的影响
正面作用:
提高切削速度可减少切屑与刀具前刀面的摩擦,降低积屑瘤生成概率,改善齿面粗糙度(如滚齿时 v 从 80m/min 提升至 120m/min,表面粗糙度 Ra 可从 3.2μm 降至 1.6μm)。
高速切削时切削热集中于切屑,减少工件热变形,提升尺寸精度。
负面风险:
速度过高(如硬质合金刀具加工 45# 钢齿轮时 v>200m/min)会加剧刀具磨损(如月牙洼磨损),导致齿形误差增大;
高速切削可能引发工艺系统振动(如颤纹),造成齿面波纹度超标。
2. 进给量(f)的影响
正面作用:
适当增大进给量(如滚齿时 f 从 0.2mm/r 增至 0.3mm/r)可提高加工效率,且适度的切削痕迹能形成储油沟槽,改善齿轮啮合润滑。
负面风险:
进给量过大(如 f>0.5mm/r)会导致切削力激增,引起工件弹性变形(如齿顶变尖、齿根过渡曲线畸变),同时加剧刀具后刀面磨损,影响齿向精度;
精密齿轮(如 6 级以上)加工时,大进给量会使表面粗糙度恶化(Ra 从 1.6μm 升至 3.2μm 以上)。
3. 切削深度(ap)的影响
分层切削的必要性:
齿轮加工(如滚齿、插齿)通常采用分层切削(粗切 ap=2~4mm,精切 ap=0.5~1mm),避免单次切削深度过大导致刀具过载崩刃;
精切时切削深度过大会残留较大加工余量,难以通过后续工序修正齿形误差(如渐开线偏差)。
二、齿轮加工切削参数优化原则
精度优先的参数调整策略
精密齿轮(5~6 级)加工:
降低切削速度(如硬质合金刀具加工钢齿轮时 v≤150m/min),减少切削热变形;
减小进给量(f≤0.2mm/r),配合小切削深度(ap≤0.3mm),通过多次精切修正齿形误差;
示例:某汽车变速箱齿轮(6 级精度)加工时,将滚齿速度从 180m/min 降至 120m/min,进给量从 0.3mm/r 降至 0.15mm/r,齿形误差从 ±8μm 降至 ±5μm。
表面质量优化:
采用 “高切削速度 + 低进给量” 组合(如 v=150~200m/min,f=0.1~0.15mm/r),配合极压切削液,降低齿面粗糙度至 Ra≤0.8μm;
剃齿工艺中,通过提高剃齿刀转速(n=1000~1500r/min)和降低径向进给量(f=0.02~0.05mm),消除滚齿残留刀痕。
抑制振动的参数调控
当工艺系统刚性不足(如悬臂式齿轮加工)时:
降低切削速度(v≤80m/min),避开共振频率;
采用 “小进给量 + 中等切削深度”(如 f=0.1~0.2mm/r,ap=1~2mm),减少切削力波动;
示例:某大型齿轮(直径>1m)加工时,将切削速度从 120m/min 降至 60m/min,进给量从 0.3mm/r 降至 0.15mm/r,颤纹缺陷发生率从 30% 降至 5% 以下。
三、切削参数优化的实施步骤与辅助措施
1. 基于 DOE 的参数试验设计
采用正交试验法(如 L9 (3⁴)),以切削速度、进给量、切削深度为因子,以齿形误差、表面粗糙度、刀具寿命为指标,确定最优参数组合。
案例:某齿轮厂通过试验发现,加工 20CrMnTi 齿轮时,最优参数为 v=150m/min、f=0.2mm/r、ap=0.5mm(精切),此时齿形误差≤±6μm,刀具寿命提升 40%。
2. 刀具几何参数协同优化
前角 γ₀:加工塑性材料(如钢)时,增大前角(γ₀=10°~15°)可降低切削力,减少变形;加工脆性材料(如铸铁)时,采用小前角(γ₀=5°~8°)避免崩刃。
后角 α₀:精切时增大后角(α₀=12°~15°),减少后刀面与加工表面的摩擦,降低粗糙度。
刃倾角 λₛ:滚齿时采用正刃倾角(λₛ=3°~5°),使切屑流向待加工表面,避免划伤已加工齿面。
3. 冷却润滑与工艺系统升级
高效冷却方案:
极压乳化液(浓度 8%~10%)适用于钢齿轮加工,可降低切削温度 20%~30%;
干切削(配合涂层刀具)用于铸铁齿轮,避免切削液导致刀具热疲劳破损。
刚性强化措施:
优化夹具设计(如增加轴向支撑),减少齿轮装夹变形;
采用电主轴(转速稳定性 ±0.1%)替代机械主轴,降低高速切削时的振动幅值。
四、典型齿轮加工工艺的参数优化要点
1. 滚齿加工
粗滚:追求效率,取 v=80~120m/min,f=0.3~0.5mm/r,ap=2~4mm;
精滚:侧重精度,取 v=60~80m/min,f=0.1~0.2mm/r,ap=0.5~1mm;
斜齿轮加工时,需同步调整滚刀螺旋升角与进给挂轮比,避免齿向偏差。
2. 插齿加工
切削速度 v=40~80m/min(高速钢刀具),进给量 f=0.05~0.15mm / 往复行程;
加工内齿轮时,减小切削深度(ap≤1.5mm),防止刀具与工件干涉。
3. 剃齿加工
剃齿速度 v=100~200m/min,径向进给量 f=0.01~0.03mm / 次,通过 3~5 次进给消除齿形误差;
剃齿刀与工件的轴交角需精确调整(通常为 10°~15°),避免齿面出现棱脊。
五、质量监控与参数迭代
在线监测:通过力传感器实时监测切削力(波动范围应<15%),振动传感器监测振幅(≤5μm),超限时自动调整参数;
离线检测:使用齿轮测量中心检测齿形误差(fₓ)、齿向误差(f₆)和表面粗糙度,根据检测结果建立参数 - 误差映射模型(如神经网络模型),实现参数的自适应优化。
|
发布时间:2025/6/13 11:38:51 点击次数:12 |
|
|
|